Sludge treatment − convective sludge dryers
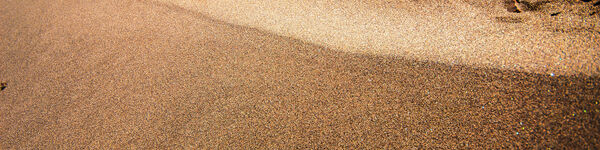
How convective sludge dryers work
Convective (or direct) sludge dryers are the most commonly used type of dryer for sewage sludge. The sludge particles are in direct contact with hot gas – air or steam – which provides the heat required to evaporate the water. Since the process demands a significant volume of air, the air is often recirculated prior to venting, to conserve energy.
The following configurations are types of convective sludge dryer:
Belt dryers comprise a conveyer belt which is fed with the dewatered sewage sludge. The sludge solids are slowly transported by the belt through a stream of heated air, generally at between 80 and 180 °C. The dried sludge may then be processed further if required, for example by crushing and pelletising, or else fed straight into the incinerator.
Belt dryers permit an additional element of process control to the usual parameters of sludge feeding rate and heat input, in that the belt speed is readily adjustable to change the dryer residence time.
Belt dryer in use at Innsbruck WwTW in Austria, Huber
Belt dryer in use at Innsbruck WwTW in Austria, Huber Source: HUBER SE / YouTube Belt dryer for chicken manure processing, Dorset GM
Belt dryer for chicken manure processing, Dorset GM Source: dorsetgreenmachines / YouTube The fluidised bed dryer employs a fixed vertical vessel with a perforated base through which hot gases (air or steam) passes. Sludge particles entering the vessel are gently agitated in a stream of pre-heated air. In this way, the air is used for both heating and mixing.
The fluidised bed configuration requires operation with backmixing of part of the dried sludge product stream with the feed to prevent the sludge going through the problematic sticky sludge drying phase
A cyclone is installed downstream of the dryer to separate the dried sludge particles from the vapour, the dust being returned to the feed. The vapour is directed to a wet scrubber, where it is purified and largely recirculated to the dryer with a small stream being vented to the atmosphere. The spent liquid from the scrubber can be returned to the head of the wastewater treatment works for treatment with the main flow.
Fluidised beds demand high temperatures, with gas temperatures of up to 900 °C, and so high energy inputs. Because of this, energy recovery is normally employed for this configuration. Fluidised beds also generate significant dust in the exhaust gas, around 0.6 to 0.7 g/m3, demanding effective cyclonic removal. On the other hand, they are simple in design, with no moving parts and are readily controlled.
Fluidised bed dryer, Andritz
Fluidised bed dryer, Andritz Source: ANDRITZ GROUP / YouTube Rotating drum – or rotary – dryers operate in a similar way to a tumble dryer for laundering. This configuration consists of a drum, several metres in length and ~2 m in diameter, which is inclined at 3–4° to the horizontal and rotates around its axis.
The drum is fitted with internal structures (referred to as fins, paddles or blades) which agitate and break up the sludge solids and help them pass along the length of the drum. The drum may also be fitted with chains suspended at its inlet and outlet, which break up the sludge and help prevent it from sticking to the walls at the dryer inlet.
Sludge introduced into the drum is scooped up in the fins as the drum rotates, usually at around 4–8 rpm, and is then released near the top of the cycle. The falling sludge particles are dried by a stream of warm air passing along the length of the cylinder in the same direction as the sludge.
Simulation of rotary dryer operation, Dynamis
Simulation of rotary dryer operation, Dynamis Source: Dynamis / YouTube Flash dryers operate at a very short residence time. The sludge is dried using a rising hot air stream, flowing at 20–30 m/s, to both suspend and dry the particles. The dried product is separated using cyclones and/or bag filters.
The dried sludge and exhaust gas temperatures are normally around 70 °C (160 °F) and 100–150 °C respectively. The exhaust gas requires treatment for deodorising (by heating) and particle removal (by scrubbing).
Flash dryers are used for industrial applications for rapidly drying slurries which have a relatively easily removed water content. They are not currently in use for sewage sludge treatment.
Example of a flash dryer for drying slurries
Example of a flash dryer for drying slurries Source: Hosokawa Micron B.V. / YouTube
Convective dryers offer the advantage of employing hot gas directly for the drying process. Since drying is often associated with a downstream thermochemical process, the waste heat in the flue gas generated from such processes can be used directly for drying.
As with all drying technologies, the rate of water evaporation increases with decreasing sludge particle size, and thus specific surface area (area per unit volume). The specific energy consumption varied between 700 and 1400 kWh per ton of evaporated water, and the specific drying rate from 0.2 kg m-2 h-1 for a flash dryer to 30 kg m-2 h-1 for a belt dryer (Arlabosse et al, 2012).