Filter presses for sludge dewatering

How filter presses work
A filter press (FP) provides sludge dewatering by pressing the sludge between a series of porous plates. The process forces water from the sludge by applying high pressures to sludge layers held between a series of 20−80 rectangular plates. The plates are recessed to allow them to be filled with sludge, and a filter cloth with an effective pore size of less than 0.1 mm fitted to each.
The FP is the only mechanical thickening or dewatering technology that is limited to batchwise (rather than continuous) operation. It is also the only dewatering technology capable of routinely achieving high concentrations of the dewatered solids cake
product – between 35 and 45% DS (dry solids) depending on the feed sludge origin and the chemical conditioning applied.
Operation of the filter press proceeds by slowly filling the recesses between the plates with the sludge before applying pressures of 7−20 bar over a period of 1−2 hours. The water is forced out of the sludge under the pressures applied, the filtrate being returned to the wastewater treatment works influent.
Air is then flushed through the system for 5−15 minutes to displace most of the residual water from the cake formed in the recesses. The filter cake may also be washed at this point to remove contaminants. The plates are then separated and the cake solids, 25−40 mm thick, allowed to fall out. The complete operating cycle of filling, filtering and emptying, and washing down the press can take up to five hours.
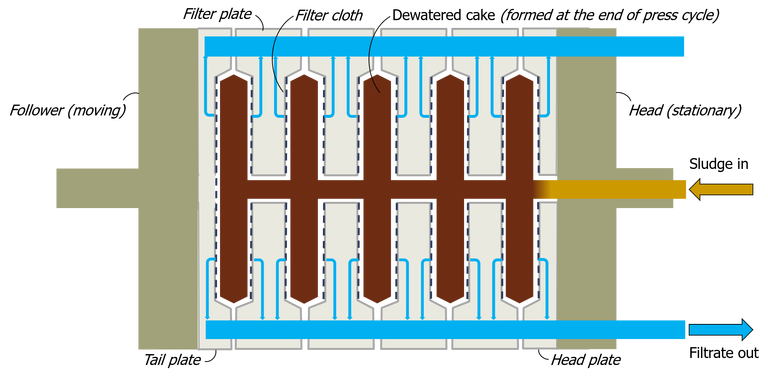
Filter press, tons per hour
A modification of the standard FP is the diaphragm/membrane press. In this technology, a flexible diaphragm is sandwiched between the filter cloth and the supporting plate. This provides additional dewatering by pressurising the diaphragm (up to ~20 bar) at the end of the pressing cycle to expand the diaphragm and provide further pressure on the cake trapped in the recesses.
The filter press has also been adapted to provide a hybrid filter press/dryer process, using a hot water system to heat the filter plates. DS concentrations above 95% have been reported from pilot trials conducted under appropriate operating conditions using this technology (Abu-Orf et al, 2007), with the cake dryness increasing with increased operational cycle time as with the conventional FP. These results relate to an unthickened thermophilic anaerobically digested sludge starting material, implying that dewatering and drying of raw sludges can be carried out in a single stage.