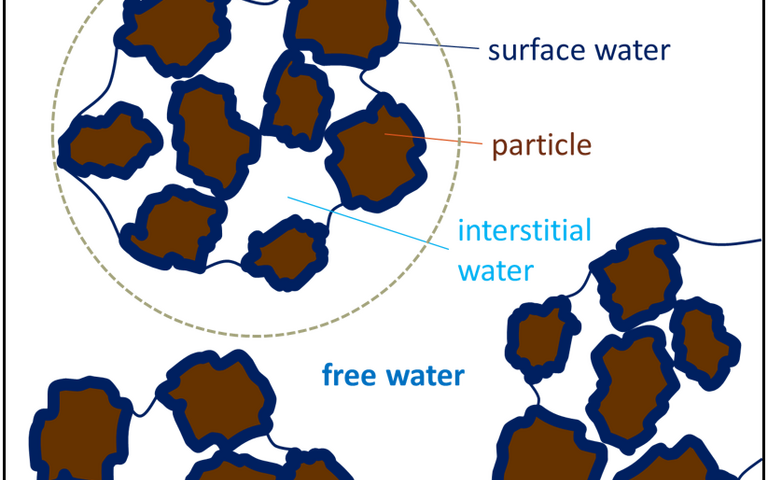
Sludge drying
An overview of sludge drying − an introduction to sludge drying theory and technologies
Your web browser is out of date.
Update your browser for better security, speed and to get the best experience on this website.
Disc dryers operate in a manner similar to paddle dryers. A series of vertical discs or rings mounted on a single shaft within a cylindrical vessel rotate in a mass of sludge passing through the vessel. The shaft and discs are externally heated by steam or hot oil. For disc dryers, unlike paddle dryers, a proportion of the dried product sludge is often recycled to avoid the formation of the sticky phase.
An overview of sludge drying − an introduction to sludge drying theory and technologies
Processes where moisture is removed from sludge as water vapour are known as 'sludge drying'
When sludge dries, it goes through three different phases as the water evaporates
Sludge drying processes operate at solids temperatures of 60-93 °C to encourage water to evaporate and leave a solid residue
Sludge drying processes are generally configured as convective, conductive, or as solar dryers
Conductive drying indirectly heats sludge by bringing the sludge particles into contact with an externally-heated surface
Convective (or direct) dryers remove moisture from sludge by bringing the sludge particles into direct contact with hot gas
Belt dryers comprise a conveyor belt which slowly transports the sludge solids through a stream of heated air
Flash dryers use a rapid stream of rising hot air which both suspends and dries the solids.
In fluidised-bed dryers the sludge particles are gently agitated and heated by a stream of upward-flowing pre-heated gas
Rotating drum dryers have a drum rotating at 4-8 RPM through which the sludge passes along with a stream of warm air
For conduction drying, the sludge is heated indirectly by bringing it into contact with a heated surface
Paddle dryers are based on externally-heated paddles rotating in the mass of sludge solids held in a stationary vessel
Solar dryers comprise large greenhouses in which sludge is dried under the ambient conditions of the building.
Pelletizers
Conditioning is the pretreatment of sludge upstream of thickening and dewatering to promote solid-liquid separation
Thickening processes concentrate the sludge by removing part of the free water, such that the product can still be pumped
Dewatering processes mechanically remove a significant proportion of the sludge water to produce a 15-45% cake product
In sludge drying the sludge moisture is removed as water vapour by heating, generating a pelleted or powdered product
Sludge stabilisation − alkaline stabilisation, lime and solids dosing, plus anaerobic and aerobic digestion
Thermochemical methods are used to either significantly reduce the sludge solids content or pre-treat sludge upstream of AD
Sludge is the main waste stream from the treatment of wastewater